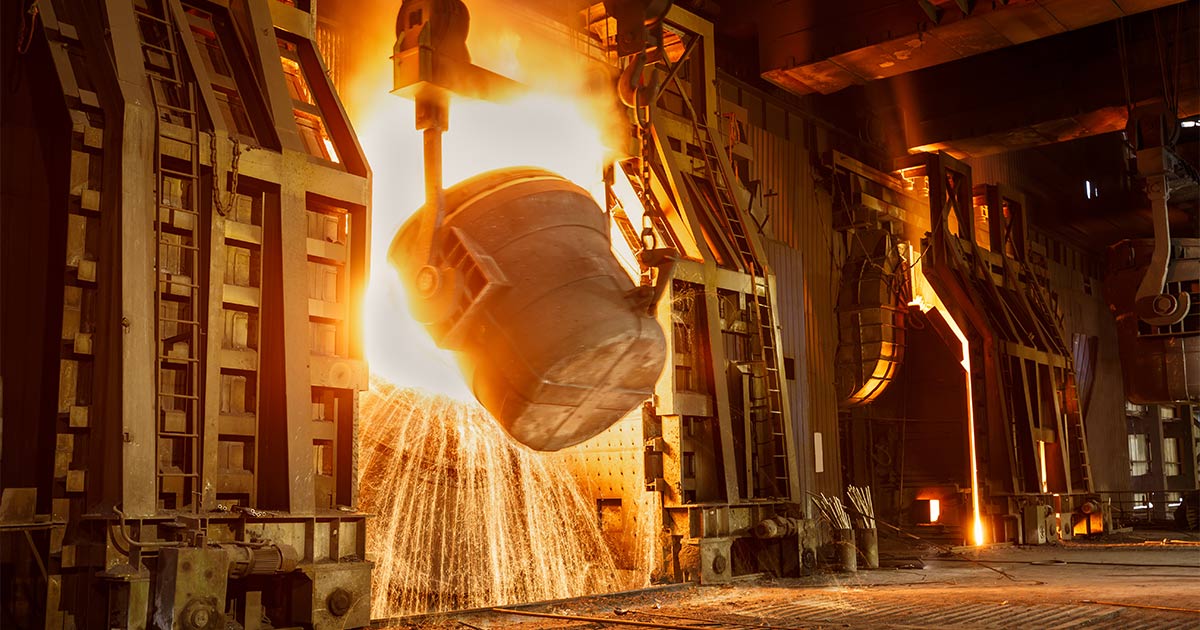
Coal has been a critical resource in the production of steel for centuries. The relationship between coal and steel production goes beyond simply providing energy; coal plays a foundational role in the transformation of raw materials into steel through a complex, multi-step process. As a key ingredient in steelmaking, coal-derived coke is essential for producing steel’s unique qualities of strength, durability, and resistance to wear. This process remains significant globally, given the reliance on steel in infrastructure, construction, manufacturing, and transportation. Understanding the role of coal in steel production offers insight into why coal remains relevant despite shifts toward renewable energy sources.
The Steelmaking Process
Steel production generally follows two primary methods: the blast furnace-basic oxygen furnace (BF-BOF) method and the electric arc furnace (EAF) method. The BF-BOF method is the traditional process and the most coal-intensive, while the EAF method is less dependent on coal, relying instead on electricity to melt scrap steel. However, around 70% of global steel production still uses the BF-BOF method, which heavily relies on coal.
Step 1: Iron Ore Reduction
The initial phase in steel production involves reducing iron ore (iron oxide) into molten iron. This reduction process requires a carbon source to react with the oxygen in iron ore, which is where coal-derived coke comes in. Iron ore, coke, and limestone are added to a blast furnace, which operates at high temperatures (about 1,500°C) to initiate the chemical reactions necessary to produce iron.
Step 2: Coke Production
Coke is a solid, carbon-rich material derived from coal through a process called coking. In this process, metallurgical coal, also known as coking coal, is heated in an oven at temperatures up to 1,200°C in the absence of oxygen. This heating removes volatile substances and impurities, resulting in a dense, porous material known as coke. Coke serves as both a fuel and a reducing agent in the blast furnace, making it indispensable to the steelmaking process.
The Role of Coal-Derived Coke in Steel Production
Coke’s role in the blast furnace is vital for two main reasons: it provides the carbon needed to reduce iron ore to iron, and it generates the extreme temperatures required to melt the iron. The coke also provides a solid structure within the blast furnace, allowing gases to flow through and facilitating the chemical reactions necessary for iron production. These functions are essential in producing high-quality steel with the strength, ductility, and corrosion resistance needed for various applications.
1. Carbon Source for Reduction
In the blast furnace, coke acts as a carbon source that combines with oxygen in the iron ore. This reaction removes oxygen, resulting in molten iron. The chemical process can be simplified as follows:
Fe2O3+3C→2Fe+3CO\text{Fe}_2\text{O}_3 + 3\text{C} \rightarrow 2\text{Fe} + 3\text{CO}
This reaction requires a highly carbon-dense material, which is why coke is more effective than raw coal or other carbon sources. Without a high carbon source, the reduction process would be less efficient, resulting in lower-quality steel or higher energy requirements.
2. Heat Generation
The combustion of coke in the blast furnace produces extremely high temperatures that are necessary to melt the iron ore. These high temperatures enable the ore to separate from impurities and produce a purer form of iron, known as pig iron. The resulting pig iron is then combined with other elements like carbon and manganese to produce different types of steel, which have properties suited to various applications, from building skyscrapers to manufacturing automobiles.
Advantages of Coal-Derived Coke
The use of coke in steel production offers several advantages:
- Purity and Consistency: Coke has a high carbon content and low impurities, which allows for a more consistent and high-quality steel product.
- Structural Strength in the Furnace: Coke’s porous structure makes it physically strong, allowing it to form a stable bed within the blast furnace that supports the weight of the raw materials while allowing gases to circulate. This circulation is essential for maintaining efficient chemical reactions throughout the furnace.
- Efficient Heat Source: Coke’s high carbon content and efficiency as a fuel make it a cost-effective heat source for the high temperatures needed in steel production.
Environmental Impact of Coal in Steel Production
The BF-BOF process, while effective, is also energy-intensive and contributes significantly to global carbon emissions. Steel production is responsible for approximately 7-9% of global greenhouse gas emissions, mainly due to the reliance on coal-derived coke in the BF-BOF method. The chemical reactions in the blast furnace release large amounts of carbon dioxide, posing environmental concerns as industries seek to reduce their carbon footprint.
Recognizing these impacts, the steel industry has begun exploring alternative methods to reduce emissions, including the use of hydrogen as a reducing agent. However, this technology is still in its early stages, and the infrastructure and economic feasibility for hydrogen-based steelmaking are not yet widely available. Therefore, despite the environmental drawbacks, coke remains essential for large-scale steel production in the short term.
Alternatives and Innovations
The future of steel production may see significant shifts as new technologies aim to reduce the reliance on coal. Some of the most promising alternatives include:
- Hydrogen-Based Reduction: Hydrogen, when used as a reducing agent, can replace coke and reduce iron ore to produce iron. This process emits water instead of carbon dioxide, significantly lowering emissions. However, it requires renewable hydrogen and substantial modifications to existing infrastructure, so large-scale implementation is still years away.
- Biomass Substitutes: Some experiments have shown that biochar, derived from plant materials, can partially replace coke in the blast furnace. This substitute could lower emissions, but it also presents challenges in terms of scalability and cost.
- Recycling through Electric Arc Furnaces: The EAF method, which relies on scrap steel rather than iron ore, is a more sustainable approach and produces less carbon dioxide. As more recycled steel becomes available, EAFs are expected to contribute more to global steel production, helping to reduce the need for coal-derived coke.
Conclusion
Coal, particularly in the form of coke, plays a foundational role in steel production. It serves as a critical carbon source and heat provider, making it essential for producing high-quality steel in the blast furnace process. However, the environmental impact of this method has led to growing interest in alternative technologies that can reduce or eliminate the reliance on coal. Innovations like hydrogen-based reduction and increased steel recycling offer promising paths toward a greener future for steel production. Until these technologies mature, however, coal will remain an essential resource in steelmaking, underpinning the production of steel that is vital to global infrastructure and economic development.