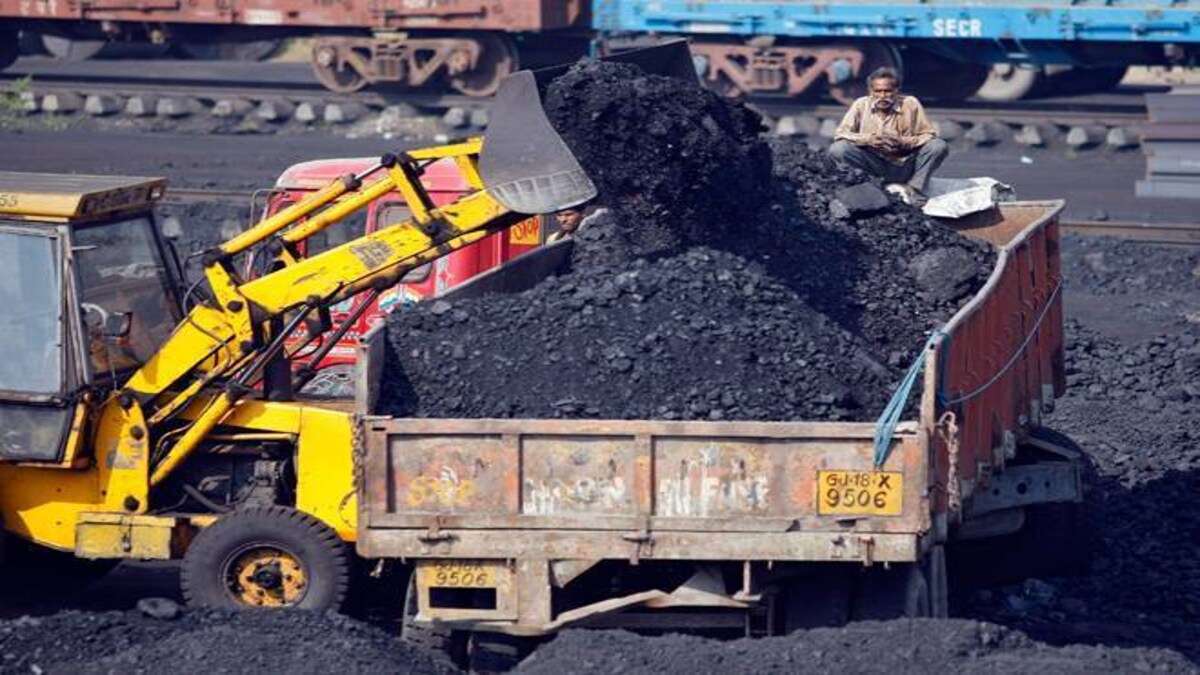
In iron and steel industries, metallurgical coal also known as coking coal is predominantly used due to its unique properties that make it indispensable for the production of high-quality steel. While several types of coal exist, each with its own characteristics and uses, metallurgical coal is specifically sought after in steelmaking because it can be transformed into coke, an essential component in the blast furnace process. The qualities of metallurgical coal, its transformation into coke, and the unique demands of steel production distinguish it as the preferred coal type for this industry. Here’s a closer look at why metallurgical coal is so critical to iron and steel production, how it differs from other coal types, and what role it plays in the steelmaking process.
1. Overview of Coal Types and Their Uses
Coal is classified into four primary types based on carbon content, energy density, and usage:
- Anthracite: The highest rank of coal, anthracite has high carbon content and energy density, but it is rarely used in steelmaking due to its brittleness and limited availability.
- Bituminous Coal: This mid-rank coal has moderate to high carbon content and includes both thermal and metallurgical types. Thermal bituminous coal is commonly used for power generation, while metallurgical bituminous coal is ideal for steelmaking.
- Sub-bituminous Coal: Lower in carbon content and energy density, this coal type is generally used for electricity generation and not for steelmaking.
- Lignite: The lowest grade of coal, lignite has high moisture content and low carbon levels, making it unsuitable for steel production.
Of these types, bituminous coal, particularly the grade suitable for coking, is the most commonly used in the iron and steel industries. It possesses the qualities needed to undergo a process called “coking,” which transforms it into a substance capable of supporting the high temperatures and chemical reactions in a blast furnace.
2. What Makes Metallurgical Coal Essential for Steelmaking?
Metallurgical coal, often a high-grade bituminous coal, is unique because it can be converted into coke through a process known as coking. Coking involves heating coal to over 1,000°C in the absence of oxygen, which drives off volatile compounds and leaves behind a porous, carbon-rich material called coke. Coke is crucial in steel production for several reasons:
- Fuel and Heat Source: Coke serves as a high-energy fuel that provides the necessary heat to reach the extreme temperatures (around 2,000°C) required to melt iron ore and convert it into molten iron.
- Reducing Agent: In the blast furnace, coke acts as a reducing agent by helping to strip oxygen from iron ore, which is essential for converting iron ore into pure iron. The carbon in coke reacts with the oxygen in iron ore, releasing it as carbon dioxide.
- Structural Support: The porous structure of coke makes it strong enough to maintain its shape under the intense heat and pressure inside a blast furnace, allowing the chemical reactions to proceed efficiently.
Without metallurgical coal, the creation of coke for traditional blast furnace steelmaking would not be possible, making it a key component in producing high-quality steel. Other types of coal, such as thermal or sub-bituminous, lack the necessary coking properties, and thus cannot be used for this purpose.
3. Differences Between Metallurgical Coal and Other Coal Types
Metallurgical coal stands out due to its high carbon content, low impurities, and caking ability, which allows it to transform into coke. Here’s how it differs from other coal types:
- Thermal Bituminous Coal: Although thermal bituminous coal has a similar carbon range to metallurgical coal, it lacks the caking ability required to produce strong, stable coke. Thermal coal is used for power generation, where exacting purity and strength standards are less critical.
- Anthracite and Sub-bituminous Coal: Anthracite, with its high carbon content, might seem suitable, but it lacks caking properties and is too brittle for coke production. Sub-bituminous coal, with its lower energy density and higher moisture content, is unsuitable for steelmaking.
- Lignite: The low carbon and high moisture content of lignite make it the least suitable type of coal for metallurgical purposes.
4. The Steelmaking Process and Metallurgical Coal
The use of metallurgical coal in steel production is a multi-step process that takes place in large steel plants, with the blast furnace-basic oxygen furnace (BF-BOF) method being the most common.
- Coke Production: In the coking process, metallurgical coal is heated in the absence of oxygen in coke ovens. This process removes volatile compounds, leaving behind coke. The coke is then transferred to a blast furnace.
- Blast Furnace Operation: In the blast furnace, coke serves as both the fuel and the reducing agent. Iron ore, coke, and limestone are loaded into the furnace, and hot air is blown in. The coke combusts, producing heat and carbon monoxide, which facilitates the chemical reduction of iron ore (iron oxide) into molten iron.
- Steel Conversion: Once molten iron is produced, it is transferred to a basic oxygen furnace, where it is mixed with scrap steel and pure oxygen. This process removes any remaining impurities, producing high-quality molten steel.
Approximately 70% of the world’s steel is produced using the BF-BOF process, making metallurgical coal indispensable. Alternative methods, like electric arc furnace (EAF) steelmaking, which primarily uses recycled scrap steel and requires less coal, are growing in popularity, but blast furnaces remain dominant in primary steel production.
5. Market Demand and Environmental Impact
The global demand for steel, especially in emerging economies, drives the demand for metallurgical coal. Countries like China and India, which have extensive steelmaking industries, are among the largest consumers of metallurgical coal. The market for metallurgical coal is closely linked to infrastructure projects, automobile manufacturing, and construction, all of which rely on high-quality steel.
However, the environmental impact of using metallurgical coal is a significant concern. The combustion of coke in steelmaking releases substantial amounts of carbon dioxide (CO₂), contributing to greenhouse gas emissions. Approximately 7-9% of global CO₂ emissions stem from the steel industry, and metallurgical coal is a major contributor. Innovations are being explored, such as hydrogen-based reduction and electric arc furnaces using renewable energy, but the technology and cost barriers mean that metallurgical coal will likely remain crucial to steel production for the foreseeable future.
6. Future Prospects and Alternatives
While metallurgical coal remains indispensable for modern steelmaking, the industry is actively seeking alternatives to reduce emissions and reliance on coal:
- Hydrogen-Based Steelmaking: Hydrogen can act as a reducing agent in steelmaking, eliminating the need for coke. Although promising, this technology is still in the early stages of development and faces challenges related to cost and infrastructure.
- Electric Arc Furnaces (EAF): EAFs melt scrap steel using electricity, significantly reducing the need for coal in steel production. While EAFs produce lower emissions, they rely heavily on scrap metal availability and renewable electricity sources.
- Carbon Capture and Storage (CCS): CCS technology can capture CO₂ emissions from blast furnaces, reducing the environmental impact of metallurgical coal. While CCS holds promise, it is an expensive and resource-intensive solution that is not yet widely adopted.
Conclusion
In summary, metallurgical coal, primarily in the form of bituminous coking coal, is the type of coal most widely used in iron and steel industries due to its ability to be transformed into coke. This transformation is crucial for the blast furnace process, where coke provides the heat, support, and reducing capability necessary to produce molten iron, the foundational element of steel. Despite environmental concerns, metallurgical coal remains indispensable in steel production, which is essential for infrastructure, construction, and manufacturing globally. While alternative technologies are being explored, the demand for metallurgical coal in the steel industry is expected to continue for the foreseeable future.