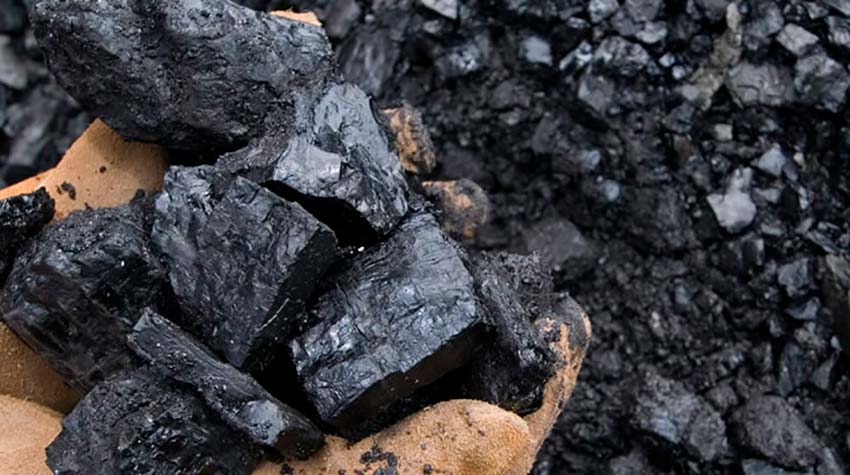
Coal, one of the world’s most abundant fossil fuels, is categorized primarily into two types based on its applications: thermal coal and metallurgical coal. These two types of coal differ significantly in terms of properties, uses, and processing requirements. Thermal coal, sometimes known as steam coal, is mainly used for electricity generation, whereas metallurgical coal, also called coking coal, is essential in the steel production process. Understanding the distinct properties and applications of each type offers insights into why both remain integral to modern industry, despite a growing shift toward cleaner energy sources.
1. Definition and Primary Purpose
Thermal Coal:
Thermal coal, or steam coal, is primarily used as a fuel source for power generation. When burned, thermal coal releases energy in the form of heat, which is used to produce steam. This steam drives turbines that generate electricity. Thermal coal is generally a lower grade of coal, meaning it has a lower carbon content, lower energy density, and higher levels of impurities compared to metallurgical coal. Its properties make it suitable for combustion in power plants but less ideal for industrial applications that require high carbon content.
Metallurgical Coal:
Metallurgical coal, also known as coking coal, is used primarily in steel production. This coal is essential for the blast furnace process in steelmaking, where it is transformed into coke—a carbon-rich material that acts as both a fuel and a reducing agent in the blast furnace. Metallurgical coal must have certain characteristics, such as high carbon content and low levels of impurities, to produce high-quality coke necessary for steel production. Due to these requirements, metallurgical coal is generally of a higher grade than thermal coal and is more expensive.
2. Chemical Composition and Properties
Thermal and metallurgical coal differ significantly in their chemical composition, which directly impacts their applications and the way they are processed.
- Carbon Content: Metallurgical coal has a higher carbon content than thermal coal, which makes it more suitable for producing the solid carbon form known as coke. This coke is essential in steel production, where it serves as a reducing agent to convert iron ore into pure iron. Thermal coal, with its lower carbon content, produces less energy and is therefore more suitable for electricity generation rather than industrial processes that demand high carbon.
- Volatile Matter: Metallurgical coal requires low levels of volatile compounds because excessive volatiles can interfere with coke formation. Low-volatile coal is also more stable when burned, making it ideal for the steelmaking process. Thermal coal, however, can have higher volatile content, which makes it easier to ignite and burn, making it suitable for use in power plants.
- Moisture Content: Thermal coal tends to have a higher moisture content than metallurgical coal. This moisture reduces its heating value, but this is acceptable in power generation where coal is simply burned to produce steam. Metallurgical coal requires lower moisture content to ensure consistent, high-quality coke production.
- Sulfur and Ash Content: Metallurgical coal must have low sulfur and ash content, as these impurities affect the quality and performance of the coke and, ultimately, the steel produced. High levels of sulfur and ash can weaken steel and lead to defects. Thermal coal can contain higher levels of these impurities since power generation is less sensitive to sulfur and ash content than steel production.
3. Processing Requirements
Thermal coal and metallurgical coal require different processing techniques due to their distinct uses and properties.
- Thermal Coal Processing: Thermal coal undergoes a relatively straightforward process before being used in power plants. After mining, it may be cleaned to remove impurities like sulfur and ash, which helps reduce air pollution when the coal is burned. The coal is then pulverized to allow for efficient combustion in power plant boilers. However, thermal coal generally doesn’t need to meet stringent quality standards, which makes its processing simpler and less expensive.
- Metallurgical Coal Processing: Metallurgical coal requires a more extensive preparation process to ensure that it can be transformed into high-quality coke. After mining, it is thoroughly washed to remove impurities, including sulfur, ash, and other minerals. This cleaning process is crucial because any remaining impurities could affect the performance of the coke in the blast furnace. Following cleaning, metallurgical coal is heated in a coking oven at temperatures above 1,000°C in the absence of oxygen. This process, known as coking, removes volatile compounds, resulting in a dense, carbon-rich product called coke, which is then used in steelmaking.
4. Applications and Market Demand
The end-use of thermal and metallurgical coal determines their market demand, price, and global trade patterns.
- Thermal Coal Applications: Thermal coal is almost exclusively used for electricity generation in power plants. As it burns, it produces heat energy, which converts water to steam. This steam then powers turbines, generating electricity. Thermal coal can also be used in cement production and a few other industrial applications that require heat but do not rely on high-carbon content. However, thermal coal’s use is primarily linked to the energy sector.
- Metallurgical Coal Applications: Metallurgical coal is essential for producing steel. Approximately 70% of global steel production uses the blast furnace-basic oxygen furnace (BF-BOF) method, where coke derived from metallurgical coal is used to reduce iron ore to molten iron. This molten iron is then refined to produce steel. Without metallurgical coal, it would be nearly impossible to achieve the high-quality steel required for infrastructure, automotive, and manufacturing applications.
Environmental Implications
Both types of coal have significant environmental impacts, but the extent and nature of these impacts vary based on how each is used.
- Thermal Coal: As a major source of carbon emissions, the burning of thermal coal in power plants contributes significantly to air pollution and global greenhouse gas emissions. The sulfur content in thermal coal also leads to sulfur dioxide (SO₂) emissions, contributing to acid rain. Many countries are now transitioning away from coal-based power generation to renewable energy sources to mitigate these impacts.
- Metallurgical Coal: The steel industry, which relies on metallurgical coal, is responsible for approximately 7-9% of global greenhouse gas emissions. While there are fewer viable alternatives for metallurgical coal in steel production compared to the energy sector, efforts are being made to reduce emissions through innovations like hydrogen-based reduction, electric arc furnaces (EAFs), and carbon capture and storage (CCS) technology.
Future Outlook and Transition
The demand for thermal coal is likely to decline as countries increasingly adopt cleaner energy sources, such as wind, solar, and natural gas. In contrast, metallurgical coal is expected to remain a vital resource for the foreseeable future due to the lack of cost-effective alternatives in steel production. However, ongoing research into hydrogen-based steelmaking and increased use of EAFs may reduce dependence on metallurgical coal over time.
Conclusion
Thermal coal and metallurgical coal differ in their chemical composition, processing requirements, and end uses, making each essential to specific sectors. Thermal coal’s primary role in power generation is declining as cleaner energy sources become more prominent, while metallurgical coal remains crucial for steel production, an industry that forms the backbone of modern infrastructure and manufacturing. As industries and governments pursue sustainable practices, these distinctions between thermal and metallurgical coal highlight both the challenges and opportunities in transitioning toward a lower-carbon future.