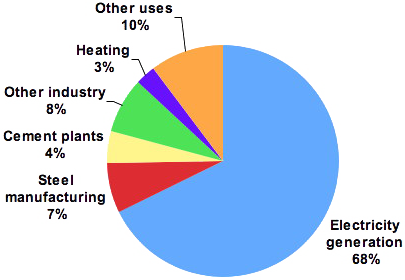
Coal is one of the world’s most important fossil fuels, utilized across various industries for energy production, heating, and as a raw material for manufacturing processes. One of its most critical uses is in steel production, where it is essential in the blast furnace process that dominates global steelmaking. Approximately 15% of global coal consumption is directed toward steel production, a figure that represents the significant role of coal in industrial manufacturing. In this context, understanding the specific percentage and reasons why coal is so integral to steel production provides insight into the resource’s global impact and highlights the environmental and economic implications of this dependency.
The Role of Coal in Steel Production
Steel is primarily produced through two major processes: the blast furnace-basic oxygen furnace (BF-BOF) method and the electric arc furnace (EAF) method. The BF-BOF process, which produces around 70% of the world’s steel, is coal-intensive, while the EAF method relies more on recycled steel and electricity, reducing its need for coal. Because of the widespread reliance on the BF-BOF method, coal plays a central role in steel production globally, making it a key factor in both the steel industry and the global coal market.
Coal’s Transformation into Coke
A substantial portion of the coal used in steelmaking is converted into coke, a carbon-dense, solid material essential for the BF-BOF steelmaking process. This transformation is achieved through coking, a process where metallurgical coal (or coking coal) is heated to high temperatures in the absence of oxygen. During this process, volatile compounds in the coal are removed, resulting in a purer, more carbon-rich product with the strength and porosity needed to facilitate reactions in the blast furnace.
In the blast furnace, coke acts as both a fuel and a reducing agent. It generates the high temperatures required to melt iron ore and reduces the iron oxides to pure iron, setting the stage for steel production. These characteristics make coke indispensable in traditional steel production, leading to high demand for coal in steelmaking operations.
Breakdown of Global Coal Usage
Globally, the primary consumers of coal are electricity generation (accounting for approximately 70% of total coal consumption), industrial applications, and steel production. Estimates show that steel production is responsible for about 15% of global coal consumption, a figure that includes direct coal use in blast furnaces and the coal-derived electricity that powers electric arc furnaces (EAFs).
To break it down further:
- Electricity Generation: Roughly 70% of global coal use is dedicated to generating power, particularly in countries with limited renewable energy sources or heavy industrial sectors.
- Steel Production: Approximately 15% of coal is used for steel, with about 1.5 tons of coal needed to produce one ton of steel via the BF-BOF method. This percentage varies slightly based on regional practices and the balance between the BF-BOF and EAF methods.
- Other Industrial Uses: The remaining 15% of coal use is distributed across industries such as cement production, chemical manufacturing, and other sectors requiring high-energy processes.
Regional Variations in Coal Use for Steel Production
The percentage of coal used for steel production can vary significantly by region, largely due to differences in industrial practices, access to raw materials, and energy infrastructure. Some countries, particularly China, India, and Japan, rely heavily on coal for both power generation and steel production. These countries produce a large percentage of the world’s steel and are major coal consumers, resulting in a significant portion of their coal usage being dedicated to steelmaking.
In contrast, countries with more renewable energy sources and advanced recycling industries, such as the United States and parts of Europe, use a higher proportion of electric arc furnaces. These EAFs depend on scrap steel and electricity, making them less reliant on coal, which reduces the share of national coal use allocated to steel production.
Environmental Impact of Coal Use in Steel Production
Steel production is one of the most carbon-intensive industrial processes globally, primarily because of the dependence on coal in the BF-BOF process. Producing one ton of steel through the BF-BOF method generates roughly 1.8 tons of carbon dioxide (CO₂), making the steel industry a significant contributor to global greenhouse gas emissions. As the world produces over 1.8 billion tons of steel annually, emissions from coal use in steelmaking represent a substantial environmental challenge.
In recent years, there has been a push toward reducing coal reliance in steel production through several key approaches:
- Hydrogen-Based Reduction: Hydrogen can serve as a cleaner alternative to coal-derived coke in the reduction of iron ore, emitting water vapor instead of carbon dioxide. This technology is still in development but promises to transform steel production if implemented widely.
- Electric Arc Furnaces (EAFs): EAFs, which rely on recycled steel and electricity rather than coal, generate far fewer emissions and can be powered by renewable energy. Expanding the use of EAFs is one strategy to lower the carbon footprint of steel production, though it depends on the availability of scrap steel and the capacity of electricity grids.
- Carbon Capture and Storage (CCS): CCS technology can capture CO₂ emissions from traditional blast furnaces and store them underground. While CCS can reduce emissions, it is still an expensive technology and has yet to be widely adopted due to technical and economic challenges.
- Improving Energy Efficiency: Increasing energy efficiency in coal-powered steel plants can help lower coal consumption and reduce emissions, though this does not entirely replace coal use.
Economic and Policy Implications
As industries and governments prioritize carbon reduction, there is a growing push to reduce coal use in steel production. This shift is driven by both environmental concerns and economic factors, as coal’s continued use could incur higher costs due to carbon taxes, regulatory pressures, and the shifting energy landscape. However, given that the BF-BOF method remains cost-effective and capable of producing high-quality steel at scale, coal is expected to remain important in the steel industry for the foreseeable future.
Governments are increasingly incentivizing the use of greener technologies through subsidies, research grants, and carbon pricing, accelerating the exploration of alternative steelmaking methods. However, transitioning away from coal will require significant investment and coordination across industries and governments, as the infrastructure for hydrogen-based steelmaking, EAFs, and CCS technologies is still in its early stages.
Conclusion
Coal plays an essential role in steel production, with approximately 15% of global coal consumption allocated to this purpose. Despite environmental concerns, coal-derived coke is critical for the blast furnace method that dominates global steel production. As industries seek more sustainable practices, alternatives like hydrogen reduction and electric arc furnaces offer promising paths forward, though they require substantial investment and technological advancement to replace coal fully. For now, coal remains a cornerstone of the steel industry, underscoring the need for balanced solutions that address both environmental and economic considerations.